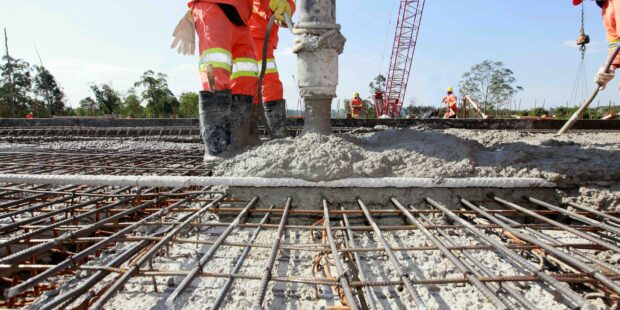
The goal of each blend is to meet the needs for strength, durability, workability, sustainability and economy
By Ken Hover
Over 20 billion cubic yards of concrete are produced per year, or about six quarts of concrete batched every single day, for each man, woman and child on this planet. No other manufactured material comes close to the annual volume of concrete production. Our industry’s biggest current problems, environmental impact and sustainability, are magnified by the sheer volumes of cement, aggregates and in some locations, the water needed to produce this essential component of the built environment. Efficient architectural and structural design, intelligent mixture-proportioning and productive construction methods are needed to make every cubic yard count.
Millions of particles of natural rocks and sand are glued together to make a single cubic yard of the artificial rock we call “concrete.” The most common glue or “paste” is made of dry Portland cement powder mixed with water. This amazing paste initially lubricates the aggregates so they slide past each other in workable concrete, soon transitioning into a strong adhesive. On the job site that transition appears as slump loss, setting and strength gain, driven by “hydration” (the chemical reaction between cement and water). Concrete appears to stiffen because it dries, but premature drying robs the cement of the water needed to develop strength. Proper curing minimizes water loss and provides water to the cement.
Most folks think concrete is the most solid material imaginable, but it is a porous, absorptive material. The rocks and sand are variably porous, with a porous zone where the aggregate surfaces contact the hardened paste. Most concrete porosity, however, is the residual volume of mix water and any other water intentionally or unintentionally added to the fresh concrete. In general, the greater the concrete’s porosity the lower the strength and durability, and the shorter its service life.
Concrete’s pores allow rainwater, melted ice and snow, seawater, deicing salt, sulfates, alkalis, oxygen and carbon dioxide to penetrate deep into the concrete, resulting in common forms of concrete deterioration like freezing and thawing, scaling and corrosion of reinforcing steel. Reducing concrete’s porosity is the key to stronger, more durable concrete with a longer service life.
…we must recognize that while concrete is ordered, delivered, placed, argued about and paid for by volume (typically expressed in cubic yards in the U.S.), concrete is produced by weight.”
Good quality aggregates are typically stronger, stiffer and more durable than the surrounding hardened cement paste, so paste generally controls strength, durability and service life. Effective mix design can result from increasing aggregate volume while decreasing cement and water volume. The payoff is improved structural performance, reduced carbon footprint and economy.
For any given batch weight of dry Portland cement, the paste adhesive becomes more concentrated, stronger and less porous with lower water content. Workability improves as water content increases but added water dilutes the paste, yielding weaker, less durable hardened concrete. The weight of water divided by the weight of cement (called the “water-to-cement ratio,” or “w/c”) is, therefore, a key index of concrete performance. The prevailing commercial building code in the United States limits w/c to 40 lb of water per 100 lb of cement for reinforced or prestressed concrete exposed to seawater or deicing salts in-service.
An expensive, high shrinkage, unsustainable way to maintain strength while achieving workability is to increase both the weight of cement and the weight of water in the mix, keeping their ratio constant. A more effective solution is to blend appropriate combinations of aggregate sizes, shapes and textures along with supplementary cementitious materials to promote workability at lower water content. Normal, mid-range, or high-range water-reducing admixtures (superplasticizers) can either maintain workability with a reduced water content or increase workability without increasing water.
The goal is to simultaneously meet the needs for strength, durability, workability, sustainability and economy. In meeting this challenge we must recognize that while concrete is ordered, delivered, placed, argued about and paid for by volume (typically expressed in cubic yards in the U.S.), concrete is produced by weight.
A known total weight of fresh concrete is loaded into the truck that has been calculated to yield the volume printed on the delivery ticket. Adjustments to improve concrete mixture performance must therefore preserve the delivered volume of the product. Any adjustment to the batch weight of a single ingredient must be volumetrically balanced with an adjustment to at least one other ingredient. There can be no independent changes to a single ingredient. Each concrete mixture ingredient has its impact on the performance of fresh or hardened concrete, and each influences the behavior of all other ingredients. I am often reminded that in a concrete mixture, “Everything affects everything else,” as stated by chemist Floyd Slate.
Ken Hover is professor emeritus of Civil and Environmental Engineering at Cornell University.