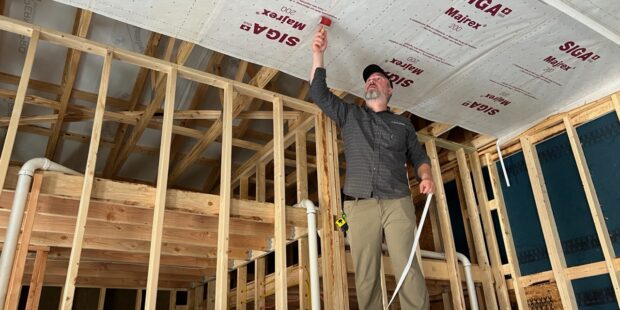
Managing building durability, performance and comfort with water, air, vapor and thermal control layers
By Travis Brungardt
In a time where technology is constantly providing new opportunities for greater convenience and control, why is it that we in the building industry are referencing the lessons of ancient Egypt and the Energy Crisis of the late 1970s? Because the laws of thermodynamics, energy flow and gravity are timeless, that’s why.
Today’s “building science” is essentially high school-level physics applied to the methods and materials that make up our building enclosures. It’s no more complex than the wind catchers of ancient Persia or the insulation and solar advances of the seventies. At least the foundational principles that govern our understanding and subsequent application of building science remain that simple. What gets all the fuss is the complexity of knowing what materials and methods to apply both where and when.
Let’s take a minute to unpack what we mean when we say “building science” since basic physics applied to the building is still a little broad. When we hear someone mention BS* (heretofore building science), they are very likely to address what is known as the “control layers” of water, air, vapor and thermal. Each of these can be identified on a building plan and each plays a critical role in the durability, performance and comfort of a building. After all, the whole reason we live indoors is that we want to have control rather than let the outdoor environment govern our temperature and whether we will be wet or dry.
The conversation around air control in buildings can begin with the simple understanding that since we pay to heat, cool and dehumidify homes, it’s cheaper to do so when we keep that indoor air in and the outside air out.”
Controlling water begins with putting a roof on the building and a drainage system for the foundation below. Where we get into the building science details is where we start talking about rainscreens, drainage and back venting of claddings or the myriad water/weather resistant barriers (WRB) strategies. The plot thickens for BS nerds when we start discussing the vapor permeability of those WRBs, mechanically fastened, self-adhered or fluid-applied.
Similarly, the conversation around air control in buildings can begin with the simple understanding that since we pay to heat, cool and dehumidify homes, it’s cheaper to do so when we keep that indoor air in and the outside air out. As you dive into how to do this more effectively you’ll rapidly run into a whole host of material options from spray foams, caulks and sealants to rolls of sheeting and fancy tapes.
You can’t avoid the building scientists anymore with building codes enforcing minimum air-tightness standards measured by HERS raters with blower doors seeking specific “ACH50” rates. That’s air changes per hour at 50 pascals of pressure: a uniform standard to measure how many times the air in the building would be replaced in its entirety with outdoor air, under a condition equivalent to a 20mph wind simultaneously applied to all sides of the building.
The BS cup runneth over when the discussion turns to vapor control, which is the non-liquid water that exists in our air, and specifically how to keep it from accumulating and condensing on surfaces inside the home. We need to manage the vapor we create indoors from showering, cooking and even breathing with methods ranging from source control (think bath fans and range hoods) to responsive membranes in our walls and ceilings and to dedicated dehumidifiers. All these options can be applied to successfully manage that vapor, but only if you understand the properties of the materials in your assemblies and apply the strategies correctly.
Thermal control seems to be one of the easiest to grasp with the simplicity of code-mandated R-value. The complexity enters into it as we consider the effective R-value of an assembly by accounting for the studs that interrupt the insulation and the thermal bridging they create. To further complicate thermal control, we have to consider the U-value, the inverse of R and the ratings of our windows and doors.
If you find this amount of jargon and detail tedious then you’re likely not yet a building science enthusiast, but you can’t ignore it and you’re already using it whether you know it or not. Regardless, the path to improving your building performance, your clients’ satisfaction and then your profitability, all runs through a better understanding of building science.
Travis Brungardt is a licensed master electrician, mechanical contractor and co-owner of Catalyst Construction.